Unlocking the Power of China Plastic Injection Molding: The Ultimate Guide for Business Success
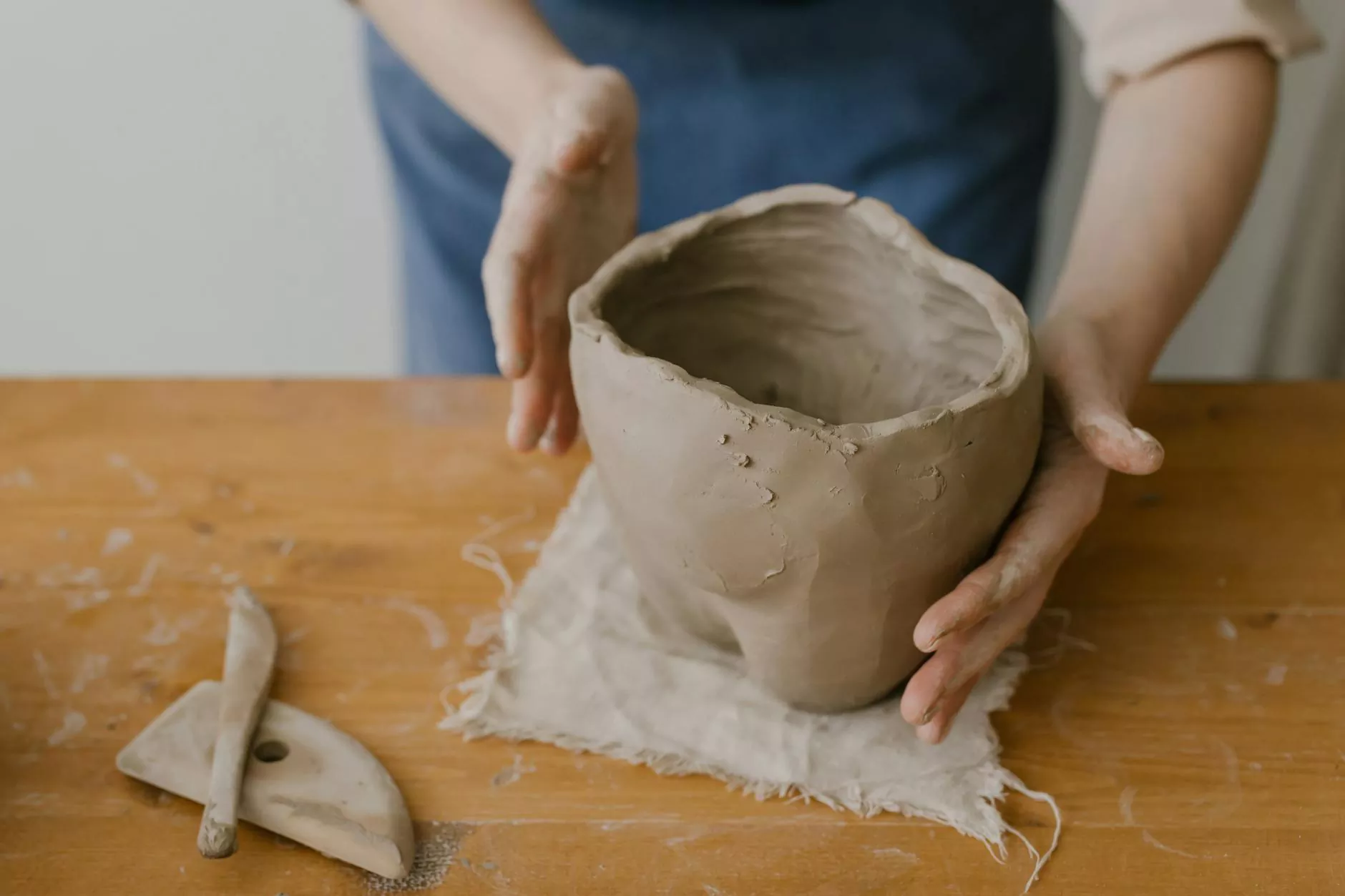
In today's highly competitive manufacturing industry, plastics injection molding in China stands out as a fundamental process empowering businesses worldwide to produce high-quality, cost-effective plastic products at scale. Whether you are a startup entrepreneur, an established manufacturer, or an investor exploring new opportunities, understanding the nuances of china plastic injection molding is crucial for strategic growth and innovation.
What Is Plastic Injection Molding? An Essential Overview
Plastic injection molding is a manufacturing process where raw plastic material is heated and injected into a precision-engineered mold cavity under high pressure. Once cooled and solidified, the plastic part is ejected, forming complex and durable components used across countless industries. This process offers unmatched versatility, accuracy, and efficiency, making it a preferred choice for mass production of plastic parts.
The Leading Role of China in Global Plastic Injection Molding Industry
Over the past decades, China has emerged as the world's manufacturing powerhouse, especially in china plastic injection molding. Thanks to a vast network of skilled manufacturers, advanced machinery, and competitive labor costs, China has become the go-to destination for companies seeking both high-quality and budget-friendly injection molding services. Leading companies like Hanking Mould exemplify the excellence achieved in this domain.
Hanking Mould: A Premier Plastic Mold Maker and Injection Mould Manufacturer in China
Hanking Mould specializes in plastic mold making and injection mould manufacturing with decades of experience. Their robust infrastructure and talented engineering team allow them to deliver custom plastic molds and injection molding services tailored to diverse industry needs. Their core strengths include:
- Precision Engineering: Ensuring every mold is crafted for perfect-fit, high-tolerance parts.
- Advanced Machinery: Utilizing state-of-the-art CNC machines, EDM equipment, and simulation software.
- Rapid Prototyping & Development: Streamlining the product development cycle for faster market entry.
- Cost-Effective Solutions: Balancing quality with affordability for customers worldwide.
The Significance of a Reliable Plastic Mold Maker in China
Choosing a dependable plastic mold maker in China is critical to ensure your projects are completed on time, within budget, and to specification. A high-caliber mold maker like Hanking Mould provides:
- Customized Mold Design: Using CAD/CAM technologies to develop molds that precisely match your product specifications.
- Material Quality Assurance: Selecting premium tool steels and plastics to maximize mold longevity and product quality.
- Prototyping & Testing: Validating design before mass production to avoid costly errors.
- Mass Production Capacity: Ability to produce large quantities with consistent quality.
The Advantages of Working with a Leading Plastic Injection Mould Manufacturer
Collaborating with an experienced plastic injection mould manufacturer like Hanking Mould provides several strategic advantages:
- High-Quality End Products: Precisely manufactured parts that meet stringent industry standards.
- Reduced Lead Time: Efficient processes and advanced machinery enable faster delivery.
- Cost Savings: Economies of scale and optimized tooling reduce per-unit costs.
- Technical Support & Innovation: Expertise-driven consultations to innovate and improve product designs.
- Flexible Production Volumes: Capability to handle both small batches and large-scale manufacturing.
Understanding the Process of China Plastic Injection Molding
China plastic injection molding involves several key steps, meticulously executed to ensure excellence:
1. Design & Engineering
Collaborate with engineers to create detailed CAD models, considering factors like structural integrity, aesthetic appeal, and manufacturability.
2. Mold Fabrication
The mold is precisely machined from high-grade steel, ensuring durability and precision. Advanced techniques such as CNC machining, EDM, and rapid prototyping are typically employed.
3. Injection Molding
Raw plastic is heated until molten, then injected under high pressure into the mold cavity. Precise temperature control, pressure settings, and cycle times are essential for quality results.
4. Cooling & Ejection
The plastic part cools naturally or through cooling channels. Once hardened, the part is ejected smoothly from the mold without deformation.
5. Quality Control & Finishing
The final products undergo rigorous inspection for dimensional accuracy, surface finish, and functionality, followed by any necessary finishing touches.
Critical Factors for Successful China Plastic Injection Molding Projects
To maximize success, consider the following aspects:
- Material Selection: Choosing appropriate plastics such as ABS, polypropylene, or engineering plastics based on application needs.
- Precision Mold Design: Incorporating cooling channels, ejection systems, and gating to optimize cycle time and quality.
- Process Optimization: Fine-tuning parameters for consistent production.
- Supplier Reliability: Partnering with experienced manufacturers like Hanking Mould ensures reliable supply chains and technical support.
- Post-Processing: Secondary operations such as assembly, painting, or surface treatment to enhance product functionality and aesthetics.
Why China Continues to Lead in the Injection Molding Industry
Several factors contribute to China's dominance in china plastic injection molding:
- Cost Advantages: Lower manufacturing and labor costs without compromising quality.
- Massive Industry Ecosystem: A comprehensive network of raw material suppliers, machinery manufacturers, and skilled labor.
- Technological Advancement: Ongoing innovations in mold design and injection techniques.
- Export Infrastructure: Well-developed logistics and transportation channels facilitate global distribution.
- Government Support & Policies: Incentives for technological innovation and export growth.
How to Choose the Right Partner for Your China Plastic Injection Molding Needs
Partnering with a trustworthy manufacturer is the cornerstone of successful projects. Consider these factors:
- Experience & Track Record: Look for companies with proven industry experience, like Hanking Mould.
- Certifications: ISO, ASTM, or other relevant quality certifications ensure standards compliance.
- Manufacturing Capabilities: State-of-the-art machinery and skilled personnel.
- Customization & Flexibility: Ability to handle custom designs, rapid prototyping, and complex molds.
- Customer Service & Communication: Clear communication channels, technical support, and after-sales service.
The Future of China Plastic Injection Molding Industry
The industry is rapidly evolving with advancements such as automation, Artificial Intelligence (AI), and Industry 4.0 integration. These innovations promise increased efficiency, improved quality, and reduced costs. Additionally, sustainable manufacturing practices are gaining momentum, emphasizing eco-friendly materials and energy-efficient processes, aligning China’s plastic injection molding sector with global environmental standards.
Conclusion: Elevate Your Business with Expert China Plastic Injection Molding
In summary, the china plastic injection molding industry offers unparalleled opportunities for companies aiming to scale their product lines efficiently and economically. Partnering with dependable manufacturers like Hanking Mould guarantees not only high-quality molds and parts but also a strategic advantage in a competitive marketplace. With technological advancements and a robust manufacturing ecosystem, China remains at the forefront of plastic mold making and injection molding excellence, paving the way for future innovations and enhanced global competitiveness.
Now is the time to leverage the benefits of china plastic injection molding to propel your business forward, ensuring quality, efficiency, and cost-effectiveness in every project.