The Ultimate Guide to Plastic Injection Molding Products
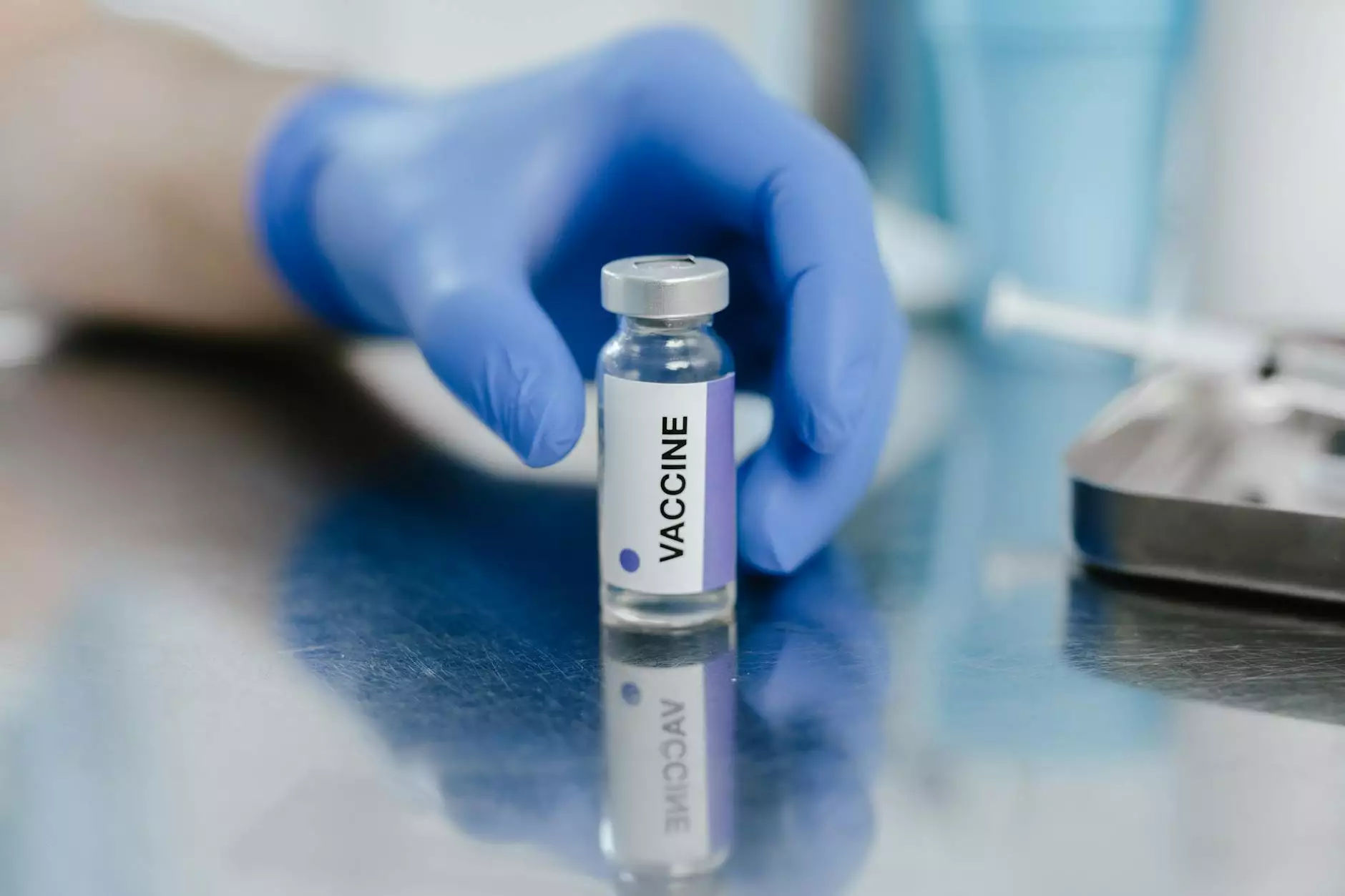
Plastic injection molding products are at the forefront of modern manufacturing, enabling companies to create precise, durable, and complex components at scale. This process is not just about mass production; it's also a testament to innovation in design and efficiency in resource management. In this comprehensive guide, we will explore the intricacies of plastic injection molding, including its advantages, applications, and the future of this transformative technique.
Understanding Plastic Injection Molding
Plastic injection molding is a production process used to create parts by injecting molten material into a mold. This method is widely appreciated for its ability to produce intricate shapes with high precision and repeatability. Here’s a closer look at how the process works:
- Material Selection: Commonly used materials include thermoplastics and thermosetting polymers. They are chosen based on the desired properties of the final product.
- Injection Molding Machine: This machine consists of a hopper, a heated barrel, and a mold. It melts the plastic pellets and injects them into the mold under high pressure.
- Cooling and Solidification: Once injected, the plastic is cooled, allowing it to solidify and take the shape of the mold.
- Mold Removal: After solidification, the mold is opened, and the finished product is ejected.
The Advantages of Plastic Injection Molding Products
Investing in plastic injection molding products provides a multitude of benefits that can significantly enhance manufacturing operations:
- High Efficiency: Once the mold is created, the production rate is extremely high, making it ideal for large quantities.
- Precision Accuracy: This method allows for tight tolerances and complex geometries that are challenging with other methods.
- Cost-Effectiveness: Although the initial cost for mold creation can be high, the cost per unit decreases significantly with mass production.
- Material Versatility: Many types of plastics can be used, offering diverse properties and functionalities.
- Minimal Waste: Because excess material can often be recycled and reused, waste is minimized, contributing to sustainability.
Applications of Plastic Injection Molding Products
The applications of plastic injection molding products are vast, spanning various industries:
1. Automotive Industry
In the automotive sector, plastic injection molding is used to manufacture components such as dashboards, panels, and trim pieces that require durability and precise fit. The lightweight nature of plastic helps improve fuel efficiency while maintaining performance.
2. Consumer Electronics
Plastic housings and internal components of consumer electronics like smartphones, laptops, and home appliances are often produced through injection molding, ensuring they are both aesthetically pleasing and functional.
3. Medical Devices
The medical industry utilizes plastic injection molding for producing components that require meticulous cleanliness and tight tolerances, such as syringes, surgical instruments, and enclosures for electronic devices.
4. Packaging Industry
From bottles to containers, plastic injection molding is instrumental in creating innovative packaging solutions that are lightweight, strong, and often recyclable.
5. Furniture and Home Goods
Plastic parts are ubiquitous in furniture and home goods, including chairs, tables, and storage solutions, where durability and design are paramount.
Choosing the Right Plastic Injection Molding Partner
Finding the right partner for your plastic injection molding needs is crucial for ensuring product quality and efficiency. Here are factors to consider when choosing a manufacturer:
- Experience and Expertise: Look for a partner with a proven track record in your specific industry.
- Quality Assurance Protocols: Ensure they have strict quality control measures in place to maintain high product standards.
- Technology and Equipment: Advanced machinery and technology can enhance precision and efficiency.
- Customization Capabilities: Choose a partner willing to work with you on tailored solutions and bespoke designs.
- Customer Support: A responsive and supportive customer service team is essential for a smooth collaboration.
The Future of Plastic Injection Molding Products
The landscape of plastic injection molding products continues to evolve as technology advances. Here are some trends shaping the future:
1. Sustainable Manufacturing
With increasing awareness of environmental issues, the industry is moving towards biodegradable plastics and sustainable practices, including the recycling of scrap material.
2. Advanced Materials
Research into new materials, including composites and recycled plastics, is opening doors to innovative products with enhanced properties.
3. Automation and AI
The incorporation of robotics and AI in the injection molding process leads to greater efficiency, reduced labor costs, and minimized human error.
4. Customization and Short Runs
As consumer preferences shift towards personalized products, manufacturers are adapting to smaller batch sizes and customized designs without significant cost penalties.
Conclusion
The world of plastic injection molding products is dynamic, innovative, and crucial for numerous industries. Understanding the process, benefits, and applications can empower businesses to leverage injection molding in their product development. As technology and material science advance, the potential for future applications seems limitless. Investing in high-quality injection molding products not only ensures efficiency and cost-effectiveness but also plays a critical role in sustainable manufacturing practices that benefit both businesses and the planet.
At DeepMould.net, we are committed to providing exceptional plastic injection molding products that meet the rigorous demands of various industries. Partner with us to transform your ideas into reality through cutting-edge manufacturing solutions.